The scent of fresh-cut wood fills the air as I step into the lumber aisle—a mixture of excitement and intimidation washes over me. Rows upon rows of plywood sheets tower above, each one promising potential but also posing questions. I recall my early woodworking days when choosing the right plywood felt like navigating a maze without a map. If you've ever felt overwhelmed in the lumber section, you're not alone. With plywood prices soaring, making the wrong choice can be an expensive mistake. Let me share the five mistakes I've learned to avoid when buying plywood, so you can save both time and money.
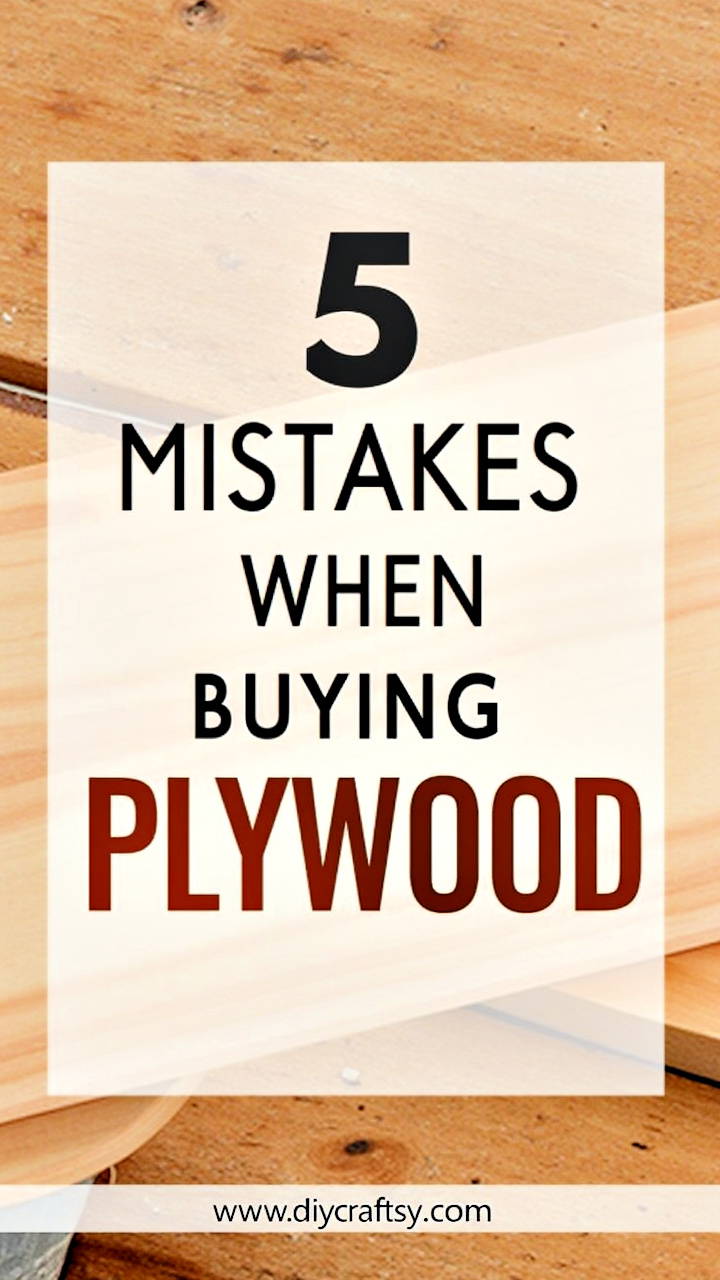
Mistake #1: Choosing the Wrong Type of Plywood
Understanding the different types of plywood is crucial to selecting the right one for your project.
Have you ever grabbed the first sheet of plywood you saw, thinking it would work for your project, only to realize later it was all wrong? I sure have. The first time I attempted to build a bookshelf, I didn't pay attention to the type of plywood I bought. The result was a sagging, unattractive mess that barely held together.
Plywood comes in various types, primarily divided into construction-grade and finish-grade categories. Understanding the difference can save you a lot of hassle.
Construction-Grade Plywood
This type is often labeled as CDX and is designed for structural purposes like subflooring and exterior sheathing. It's rough, filled with knots, and not suitable for fine woodworking projects. Using it for furniture or cabinetry will likely lead to disappointing results.
Finish-Grade Plywood
This is what you want for furniture, cabinetry, or any project where appearance matters. Within this category, you'll encounter options like:
- Hardwood Plywood: Features a veneer of hardwood species like oak, maple, or birch, offering a beautiful grain suitable for staining or clear finishes.
- Softwood Plywood: Usually made from pine or fir, it's less expensive but may have more knots and defects.
- Composite Materials: Includes melamine and MDF. Melamine has a plastic coating over particleboard, ideal for shelves and surfaces that need a clean, finished look. MDF is smooth and great for painting but heavy and not moisture-resistant.
I learned that selecting the right type of plywood depends heavily on the project's requirements. Now, I take the time to match the plywood type to the end use, which has made a world of difference in the quality of my builds.
Mistake #2: Buying the Wrong Size or Thickness
Selecting the appropriate size and thickness of plywood ensures structural integrity and cost-effectiveness.
Standing in front of a stack of plywood, the temptation to opt for thinner, cheaper sheets is real. I once thought using 1/2-inch plywood instead of 3/4-inch would save money without compromising much on strength. Boy, was I wrong.
The thickness of the plywood plays a crucial role in its strength and stability. Here's what I've learned:
3/4-Inch Plywood
Ideal for structural components like shelves, tabletops, and cabinet carcasses. It provides the rigidity and strength needed for load-bearing applications. Despite being labeled as 3/4-inch, it's often slightly less due to milling—usually around 23/32 inches.
1/2-Inch Plywood
Suitable for drawer boxes, cabinet backs, and areas where full thickness isn't required. It’s lighter and easier to handle but not as strong. When used in the right context, it can save you money without sacrificing too much strength.
1/4-Inch Plywood
Best for backing panels, lightweight drawer bottoms, and decorative applications. It's not structural and should not be used where strength is needed.
Additionally, consider the actual dimensions of the plywood sheets. While a standard full sheet is 4x8 feet, buying smaller project panels like 2x4 feet might seem convenient but can cost significantly more per square foot. If transportation is a concern, many stores will cut the plywood for you, or you can bring along a circular saw to make cuts in the parking lot—I've done it, and it's a real money-saver.
Mistake #3: Ignoring Plywood Quality Grades
Plywood grades indicate the quality and appearance of the sheets, impacting both aesthetics and performance.
The first time I heard about plywood grading, my eyes glazed over. A, B, C, D—what did it all mean? After a few mishaps, I realized how crucial these grades are.
Understanding the Grades
- Grade A: Smooth, sanded surface with no knots or defects. Ideal for staining or clear finishes.
- Grade B: Solid surface with some small knots or repairs.
- Grade C and D: More knots and visible defects. Best for structural use where appearance isn't critical.
Plywood is often graded on both faces, so you might see labels like AC or BC. The first letter refers to the face veneer, and the second to the back veneer. For example, AC plywood has a high-quality face and a lower-quality back.
My Experience
I now inspect both sides of the sheet, even if one side won't be visible in the final project. Defects can affect structural integrity and may cause issues during cutting or assembly. Spending a little extra on higher-grade plywood can save headaches down the line.
Mistake #4: Not Shopping Around
Comparing options from different suppliers can lead to better quality and prices.
It's easy to fall into the habit of buying all your materials from the nearest big-box store—I did it for years. However, not all suppliers are created equal. I discovered that local lumber yards and specialty plywood suppliers often carry higher-quality products, sometimes at competitive prices.
Exploring Different Suppliers
- Big-Box Stores: Convenient but may have limited quality options.
- Local Lumber Yards: Often carry a wider variety of plywood types and grades.
- Specialty Suppliers: Offer premium products like Baltic birch plywood, which has more plies and fewer voids.
The Baltic Birch Difference
I was on the hunt for Baltic birch plywood, known for its superior quality. The big-box stores didn't carry it, but a local supplier did. Not only was the quality superior, but the price per sheet was reasonable considering the benefits.
Don't overlook online options as well. Some suppliers offer delivery, which can be a lifesaver if you don't have a vehicle capable of transporting large sheets.
Mistake #5: Not Inspecting the Sheets Before Purchase
Careful inspection ensures you get plywood free of defects that could affect your project.
There's nothing worse than getting home, ready to start your project, and finding out the plywood you bought is warped or damaged. I've been there, and it's incredibly frustrating.
What to Look For
- Flatness: Sight down the length and width of the sheet to check for warping or bowing.
- Edge Quality: Examine the edges for voids, delamination, or gaps between the plies.
- Surface Defects: Look for scratches, dents, or veneer issues that could affect the appearance.
- Consistency: If buying multiple sheets, ensure they match in color and grain pattern.
My Routine
If possible, I pull sheets from different parts of the stack to find the best ones. It might take a few extra minutes, but it ensures I get quality materials that won't cause problems later. Don't be afraid to ask for assistance if the sheets are heavy or hard to access.
Additional Tips for Buying Plywood
Helpful advice to enhance your plywood purchasing experience.
Beyond avoiding common mistakes, these additional tips can make your plywood buying experience smoother:
Plan Your Cuts
Before heading to the store, have a cut list ready. This allows you to optimize how you'll cut the sheets and might enable you to have the store make initial cuts. Planning saves both time and material.
Wear Protective Gear
Handling plywood can result in splinters. Gloves and long sleeves can save you some discomfort. Trust me, a splinter under the fingernail is no fun.
Check Return Policies
Sometimes, defects aren't visible until you start working with the material. Knowing the store's return policy can give you peace of mind. Keep your receipts and avoid cutting the plywood until you're sure it's suitable.
Consider Alternative Materials
For certain projects, materials like MDF or melamine might be more appropriate. Weigh the pros and cons based on the project's requirements. For example, MDF offers a smooth surface ideal for painting but isn't great with moisture.
Storage and Handling
- Store Flat: To prevent warping, store plywood sheets flat on a level surface.
- Avoid Moisture: Keep the sheets in a dry environment to prevent swelling or delamination.
- Use Proper Tools: A sharp, high-tooth-count blade reduces tear-out when cutting.
Conclusion
Stepping into the world of plywood doesn't have to feel like wandering in a labyrinth. By being aware of these common mistakes and taking proactive steps to avoid them, you can make informed decisions that enhance the quality of your projects. Remember, investing time in selecting the right plywood pays off in the long run. Your projects will look better, last longer, and you'll avoid the frustration and expense of working with unsuitable materials.
Happy building, and may your next project be your best one yet!